压力容器作为工业领域中***使用的关键设备,其设计质量直接关系到安全性、经济性和使用寿命。传统的设计方法主要基于标准规范和经验公式,而分析设计(AnalyticalDesign)则通过更精确的理论计算和数值模拟手段,***提升了设计的科学性和可靠性。其首要优点在于能够更准确地预测容器的应力分布和失效风险。传统设计通常采用简化的力学模型,而分析设计则借助有限元分析(FEA)等技术,综合考虑几何形状、材料非线性、载荷波动等因素,从而更真实地反映容器的实际工况。例如,在高温高压或交变载荷条件下,分析设计能够识别局部应力集中区域,避免因设计不足导致的疲劳裂纹或塑性变形,大幅提高设备的安全性。此外,分析设计能够优化材料使用,降**造成本。传统设计往往采用保守的安全系数,导致材料冗余,而分析设计通过精确计算,可以在满足强度要求的前提下减少壁厚或选用更经济的材料。例如,在大型储罐或反应器的设计中,通过应力分类和极限载荷分析,可以合理减重10%-20%,同时确保结构完整性。这种优化不仅降低了原材料成本,还减轻了运输和安装的难度,尤其对大型设备具有重要意义。 疲劳分析可以帮助识别特种设备中的潜在疲劳裂纹,从而及时进行修复,防止设备事故的发生。浙江压力容器ANSYS分析设计收费明细
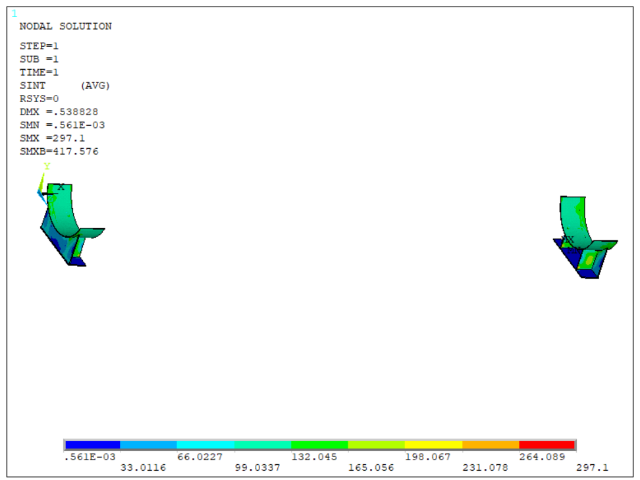
第四代核电站的氦气-蒸汽发生器(设计温度750℃)需评估Alloy617材料的蠕变-疲劳损伤。按ASMEIIINH规范,采用时间分数法计算蠕变损伤(Larson-Miller参数法)与应变范围分割法(SRP)计算疲劳损伤。某示范项目通过多轴蠕变本构模型(Norton-Bailey方程)模拟管道焊缝的渐进变形,结果显示10万小时后的累积损伤D=,需在运行3万小时后进行局部硬度检测(HB≤220)。含固体催化剂的多相流反应器易引发流体诱导振动(FIV)。某聚乙烯流化床反应器通过双向流固耦合(FSI)分析,识别出气体分布板处的旋涡脱落频率(8Hz)与结构固有频率()接近。优化方案包括:①调整分布板开孔率(从15%增至22%);②增设纵向防振板破坏涡街。经PIV实验验证,振动幅值从。 上海压力容器设计二次开发咨询利用ANSYS进行压力容器的动态分析,可以模拟容器在瞬态工况下的响应,为容器的动态设计提供依据。
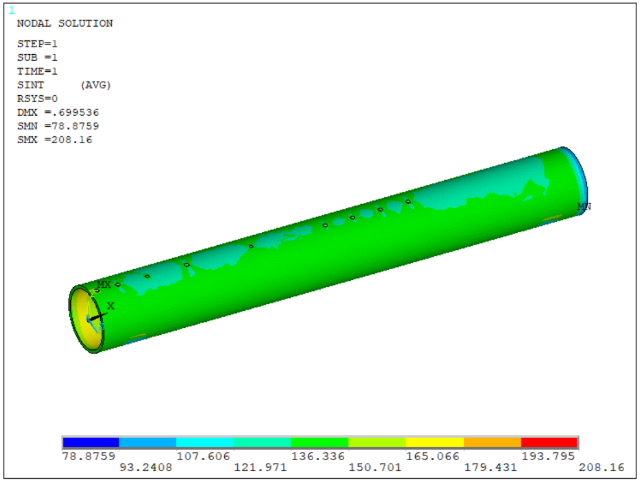
安全附件与泄放装置压力容器必须配置安全防护设施:安全阀:设定压力≤设计压力,排放量≥事故工况下产生气量;爆破片:用于不可压缩介质或聚合反应容器,需与安全阀串联使用;压力表:量程为工作压力的,表盘标注红色警戒线;液位计:玻璃板液位计需加装防护罩。安全阀选型需计算泄放面积(API520公式),并定期校验(通常每年一次)。对于液化气体储罐,还需配备紧急切断阀和喷淋降温系统。制造与检验要求制造过程质量控制包括:材料复验:抽查化学成分和力学性能;成形公差:筒体圆度≤1%D_i,棱角度≤3mm;无损检测(NDT):RT检测不低于AB级,UT用于厚板分层缺陷排查;压力试验:液压试验压力为(气压试验为)。耐压试验后需进***密性试验(如氨渗漏检测)。三类容器还需进行焊接工艺模拟试板试验。
应力分类与线性化处理方法ASMEVIII-2要求将有限元计算的连续应力场分解为膜应力、弯曲应力和峰值应力,具体步骤包括:路径定义:在关键截面(如筒体与封头连接处)设置应力线性化路径;应力分解:通过积分运算分离膜分量(均匀分布)和弯分量(线性分布);评定准则:一次总体膜应力(Pm)≤Sm一次局部膜应力(PL)≤(PL+Pb+Q)≤3Sm某反应器分析中,接管根部经线性化显示PL+Pb+Q=290MPa(Sm=138MPa),满足3Sm=414MPa要求,但需进一步疲劳评估。疲劳分析的详细流程与工程案例循环载荷下的疲劳评估是分析设计难点,主要流程如下:载荷谱提取:通过雨流计数法将随机载荷简化为恒幅循环;应力幅计算:弹性分析时需用Neuber法则修正局部塑性效应;损伤累积:基于修正的Miner法则,当Σ(ni/Ni)≥1时失效。某聚合反应器在50,000次压力循环(ΔP=2MPa)下,接管处应力幅Δσ=150MPa,对应S-N曲线寿命N=120,000次,损伤度,满足要求。在进行特种设备疲劳分析时,需要采用专业的分析软件,以提高分析的精确度和效率。
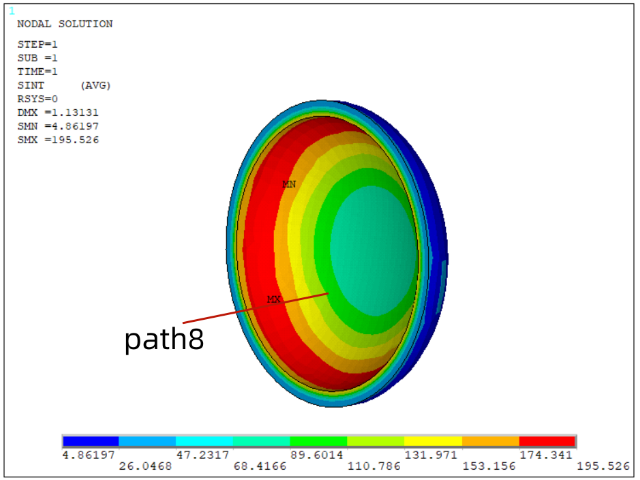
循环载荷下压力容器的疲劳失效是设计重点。需基于Miner线性累积损伤理论,结合S-N曲线(如ASMEIII附录中的设计曲线)或应变寿命法(E-N法)评估寿命。有限元分析需提取热点应力(HotSpotStress),并考虑表面粗糙度、焊接残余应力等修正系数。对于交变热应力(如换热器管板),需通过瞬态热-结构耦合分析获取温度场与应力时程。典型案例包括:核电站稳压器的热分层疲劳分析,需通过雨流计数法(RainflowCounting)简化载荷谱,并引入疲劳强度减弱系数(FatigueStrengthReductionFactor,FSRF)以涵盖焊接缺陷影响。压力容器的失效常始于高应力集中区域,如开孔、支座过渡区等。设计时需采用参数化建模工具(如ANSYSDesignXplorer)进行形状优化,常见措施包括:增大过渡圆角半径(R≥3倍壁厚)、采用反向曲线补强(如碟形封头的折边区)、或设置加强圈分散载荷。对于非标结构(如异径三通),需通过子模型技术(Submodeling)细化局部网格,结合实验应力测试(如应变片贴片)验证**结果。例如,某加氢反应器的裙座支撑区通过多目标优化,将峰值应力降低40%且减重15%。 ASME设计考虑到了容器的使用寿命,通过合理的维护和检查,确保容器的长期安全运行。压力容器ASME设计业务
通过SAD设计,可以预测压力容器在不同工作环境下的应力分布和变形情况。浙江压力容器ANSYS分析设计收费明细
当弹性分析过于保守时,可采用弹塑性分析:极限载荷法:逐步增加载荷直至结构坍塌,设计压力取坍塌载荷的2/3(ASME VIII-2)。弹塑性FEA:通过真实应力-应变曲线模拟材料硬化,评估塑性应变分布(限制≤5%)。某高压储罐通过弹塑性分析证明,其实际承载能力比弹性分析结果高40%,从而减少壁厚10%。
循环载荷下容器的疲劳评估流程:载荷谱提取:通过瞬态分析获取应力时程。热点应力确定:使用结构应力法(沿厚度线性化)或缺口应力法(考虑几何不连续)。损伤计算:按Miner法则累加,结合修正的Goodman图考虑平均应力影响。ASME VIII-2附录5-F提供了典型材料的S-N曲线,如碳钢在10^6次循环下的疲劳强度为130MPa。
长期高温运行的容器需评估蠕变损伤:本构模型:时间硬化(Norton)或应变硬化(Kachanov)方程。寿命预测:Larson-Miller参数法,如T(C+logt_r)=P,其中T为温度,t_r为断裂时间。某乙烯裂解炉出口管通过蠕变分析,确定在800℃下的设计寿命为10万小时。 浙江压力容器ANSYS分析设计收费明细
文章来源地址: http://nengyuan.huagongjgsb.chanpin818.com/sysb/shylrq/deta_29046678.html
免责声明: 本页面所展现的信息及其他相关推荐信息,均来源于其对应的用户,本网对此不承担任何保证责任。如涉及作品内容、 版权和其他问题,请及时与本网联系,我们将核实后进行删除,本网站对此声明具有最终解释权。